Written by Jim Hingst, Former Nekoosa Team Member
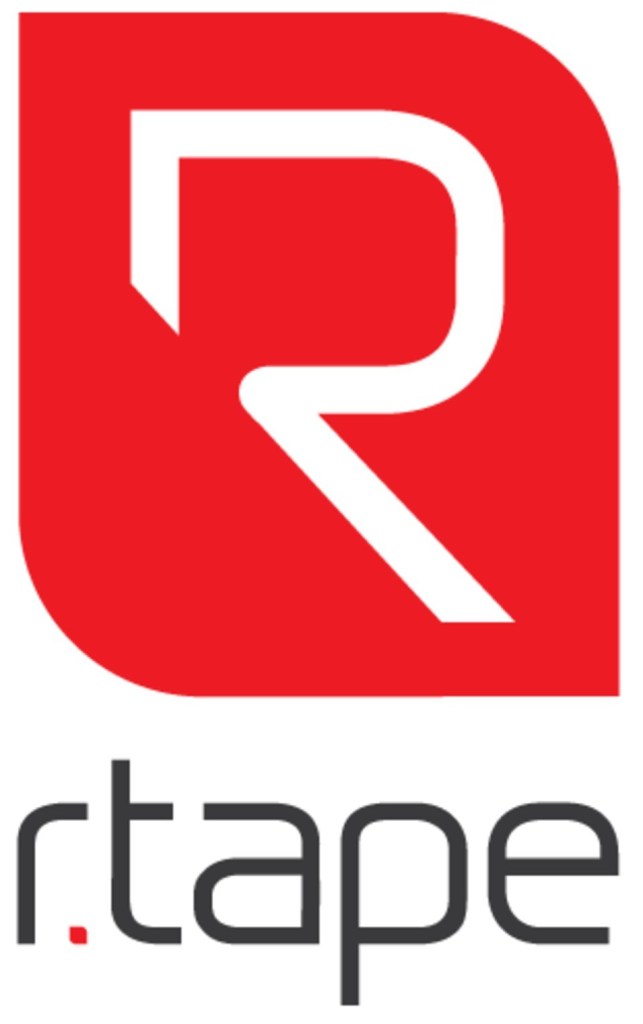
Have you ever seen silvery specs in a laminated print? This defect is called silvering. It’s caused when tiny air bubbles are captured between the adhesive on an overlaminating film and the surface of a print.
Silvering is generally most noticeable in the dark shadow areas of a print and frequently occurs when laminating UV-curable inkjet prints. There is good reason for this, too. UV inks cure immediately, so there is no time for the ink to level out. Instead of a smooth finish on the print, UV inkjet prints have a rough, velvety texture.
Ideally, the adhesives on overlaminates should be formulated to flow into that textured surface of the print. If the adhesive flows out properly, you should not have silvering problems. One way to achieve good adhesive flow out is coating the overlaminating film with a heavier coat weight. With more mass, the adhesive will more readily flow into the recesses of the textured surface of the print.
Silvering is more prevalent with polycarbonate overlaminates used on UV printed graphics. Although the adhesive on these films is thicker, it is also harder. These harder adhesives will build to higher ultimate adhesion values, but they will not wet out the way a softer adhesive will.
How to Minimize Silvering
Pressure sensitive overlaminates need pressure so the adhesive on the film properly flows out and makes complete contact with the surface of the print. Inadequate adhesive wetting can result those troublesome silvery bubbles. The amount of pressure needed in applying a laminating film can vary from film to film. Nekoosa’s polycarbonate overlaminates generally require between 40 and 100psi of pressure. If air bubbles appear, possible solutions include:
- * Increasing the nip pressure
- * Slowing the laminating speed
- * If worse comes to worse, using a little heat
Controlling the Temperature
Low shop temperatures can contribute to the occurrence of silvering. Using a little heat can help. Adjusting the heat on the top roller (from 80°F to 110°F), can help the adhesive on the overlaminate flow out better. Generally, the rule of thumb is not to use heat, unless you have a problem.
Monitoring the Laminator Speed
Pressure sensitive films usually laminate better at slower speeds. Thus, set your laminators machine speed to 3 to 5 feet per minute. Then set the machine’s pressure-control gauge, which governs the nip rollers pressure. Pressure-sensitive overlaminates require pressure so the film’s adhesive properly flows out and makes complete contact with the prints surface. Insufficient pressure can result in silvering and air-bubble formation.
Using a Sled
Thicker overlaminates, such as 5, 10 and 15 mil polycarbonate films, typically require higher pressure settings. When laminating graphics with these films, using a “sled” (which comprises a 1⁄8 in. sheet of polycarbonate or acrylic) underneath the print can increase pressure and even out the pressure across the laminator’s web.
Additional Tips to Prevent Silvering
- Don’t Stop Once You Start – Applying a laminating film to a print should be done in one continuous pass. Whatever you do, don’t stop in the middle of a print to see how it’s going. You’ll only end up with a flat spot in the adhesive, which can result in streaks and air pockets.
Test, Don’t Guess – The interaction of inks, printing systems and print media involves very complex chemistry. Incompatibility among components can adversely affect the ability of the overlaminate to adhere to the print and result in delamination. Always test and evaluate your raw materials (overlaminate, print media and mounting substrate) before a production run. When you find a winning combination, stick with it.
Curing Time – Humidity in your customer’s shop can affect their finishing job. High levels of humidity can prolong the time it takes for a print to dry. Laminating a print before it is thoroughly cured can result in solvents and moisture being trapped between the media and the overlaminate. To minimize problems caused by high humidity, shops should maintain the humidity within their shops between 20% and 50%. Before laminating, allow enough time for the print to dry. To aid drying, direct fans on printed graphics. After laminating, let prints lie flat for 24 hours before rolling to allow the adhesive system of the overlaminate to completely wet out on the surface of the print.